
Flap discs are often more comfortable to use and offer the aggressive cutting and grinding action of a grinding wheel however, they also allow for blending and finishing work, which is important when the material needs to be painted, primed, or powder-coated.
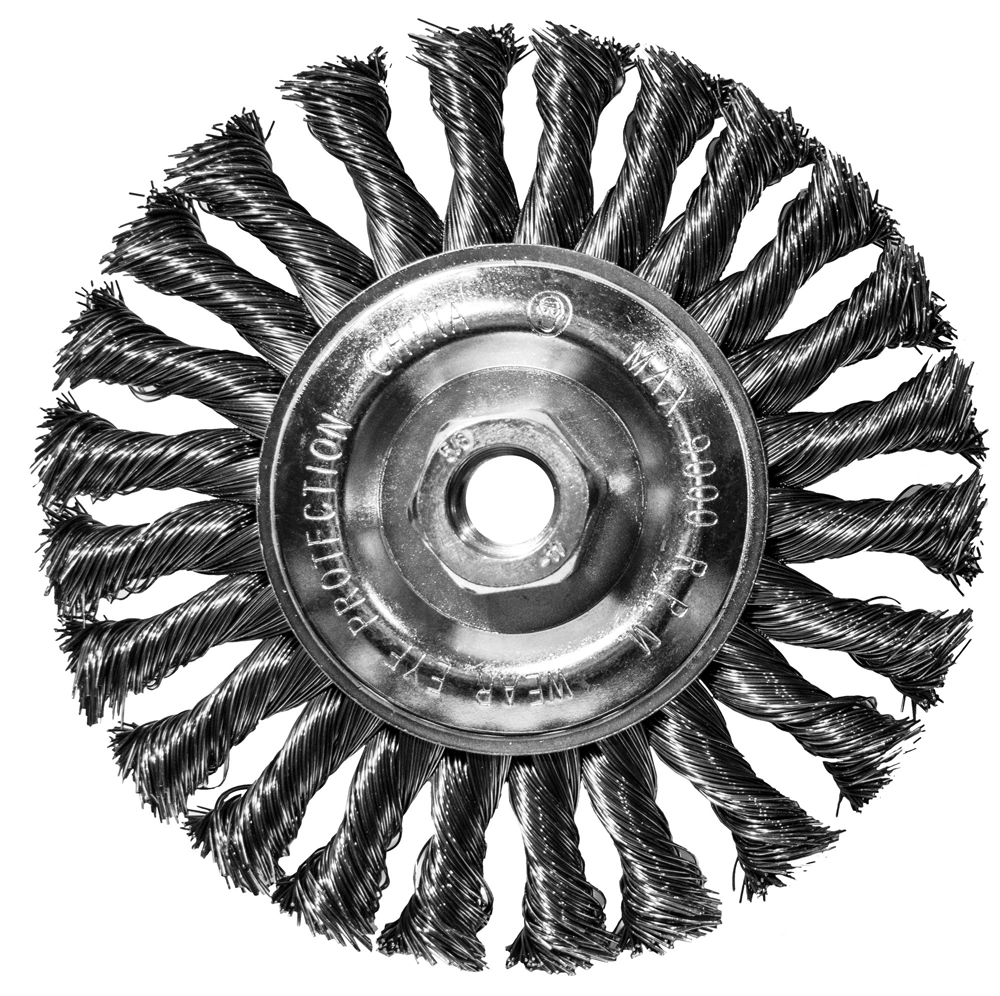
The flaps are designed and positioned to wear away as the grains deplete, exposing new, fresh, and sharp grain underneath. It is this layered construction that gives flap discs a much softer, more forgiving feel. This abrasive cloth can be cut into smaller flaps and layered radially to form a flap disc. Coated abrasives bond the abrasive grains to a backing cloth, which is most commonly a cotton, polyester, or blended backing rather than the hard grinding wheel found on bonded abrasives. These items are constructed using the same grain types as those found in bonded abrasives. They are a good choice for materials such as armored steel, structural steel, cast iron, and INCONEL ® alloys.Ĭoated Abrasives/Flap Discs. Products made with a combination of ceramic and zirconia alumina cost more, but typically provide a better overall life and material removal. Finally, this mix is molded and combined with fiberglass reinforcement layers for durability and strength.Īluminum oxide (AO) wheels are the most popular and are good for many general-purpose applications. A resinoid (organic) bonding agent is mixed with the abrasive grains. Wheels are constructed of abrasive grains, including aluminum oxide, silicon carbide, zirconia alumina, ceramic alumina, and combinations of these grains.
#Wire wheel grinder how to#
Bonded abrasives are generally more aggressive and remove material faster, requiring a skilled operator who knows how to prevent damage, gouging, and undercutting. A combination of the grain type, grain size, and bonding agents (resins and additive fillers) determines the performance of each. Here’s how these products work.īonded Abrasives/Grinding Wheels. Conversely, if an application requires that you preserve the base material during surface preparation and weld cleaning, a wire brush is still your best choice. Abrasive products are specifically designed for applications such as stock removal, edge beveling, chamfering, and weld grinding and blending. In these instances, choose an abrasive product. Note, heavy mill scale sometimes can be too much for even the most aggressive wire brush. When surface preparation or weld cleaning requires that you remove slag or mill scale, a wire brush is generally recommended. Abrasive products are designed to remove base material, whereas wire brushes are not. What you should choose depends on the requirements of the application and, of course, your personal preference.Ībrasive products and wire brushes differ in their performance and purpose. Three common tool categories are used for surface preparation and cleaning in welding applications: The right solution provides efficient, effective performance-and allows you to spend more time welding and less time cleaning and making repairs. Removing too much of the base material during preweld surface preparation can also affect weld penetration, impacting the strength and integrity of the finished weld.įor these reasons, always choose the best surface preparation and cleaning tools for the job. Removing as little material as possible between weld passes saves time and money since any material removed will ultimately need to be replaced via the most expensive consumable-the filler metal. It is critical to eliminate all inclusions and pollutants when preparing a material’s surface for welding and during interpass and postweld cleaning.

Following best practices will extend product life, ensure your safety, and increase productivity and efficiency.
